What is Preventive Maintenance?
Introduction
What exactly is preventive maintenance? Simply put, it’s the practice of regularly maintaining equipment and vehicles before problems occur.
It’s about being proactive rather than reactive. In fleet management and telematics, this approach is not just a nice-to-have; it’s essential for minimizing downtime and avoiding costly repairs down the line.
The Concept of Preventive Maintenance
Preventive maintenance involves regular, planned maintenance of your fleet to keep everything running smoothly. It’s not about fixing something after it breaks; it’s about maintaining it so well that it doesn’t break in the first place. Here’s how it stands apart:
- Corrective maintenance: This is when you fix things that have already broken. It’s necessary, but it’s often more costly and time-consuming than preventive measures.
- Predictive maintenance: This uses data to predict when a machine might fail and schedules maintenance just in time to avoid the failure.
In contrast, preventive maintenance is scheduled based on time or usage, like clocking 10,000 miles or every six months, regardless of whether signs of wear are visible. This method is particularly useful in the telematics and fleet management sector, where vehicle downtime can lead to significant disruptions and losses.
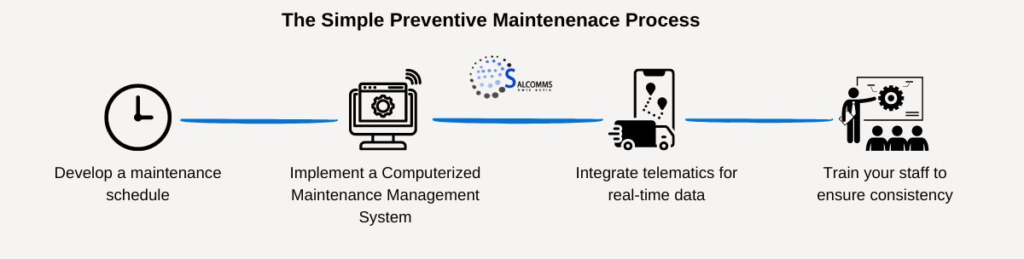
Why Preventive Maintenance is Crucial
Economic Benefits
Ever wondered how some companies manage to spend less and still keep their fleets running smoothly? The secret is preventive maintenance. Here’s how it saves you money:
- Cost savings through reduced need for repairs: Regular maintenance catches issues before they become serious problems. This means fewer big repairs and a lower chance of facing those heavy bills.
- Extending the lifespan of vehicles and equipment: Think about it like taking care of your health. Regular check-ups can lead to a longer, healthier life. The same goes for your vehicles and equipment.
Operational Benefits
Efficient operations are the backbone of any successful fleet. Here’s how preventive maintenance boosts your operations:
- Enhancing efficiency by minimizing downtime: Downtime is a profit killer. With preventive maintenance, you’re less likely to face unexpected breakdowns, keeping your vehicles on the road and your business moving.
- Improving reliability of fleet operations: Consistent maintenance ensures your fleet performs reliably. This reliability can help you maintain service quality and meet delivery schedules, which are crucial for customer satisfaction and retention.
Safety Benefits
When it comes to fleet management, safety can’t be an afterthought. Preventive maintenance not only keeps your drivers safe but also ensures you meet legal safety standards. Here’s the breakdown:
- Preventing accidents and safety incidents: Well-maintained vehicles are safer vehicles. By keeping your fleet in top shape, you reduce the risk of accidents caused by equipment failure.
- Ensuring compliance with safety regulations: Regular maintenance checks help ensure your vehicles meet safety regulations. This not only avoids fines and penalties but also protects your company’s reputation.
Types of Preventive Maintenance
Understanding the different types of preventive maintenance can help you tailor a strategy that fits your fleet’s specific needs. Here’s a quick overview:
Time-Based Maintenance
This is all about the calendar. It involves:
- Scheduling maintenance based on time intervals: Whether it’s every three months, six months, or annually, this approach keeps your maintenance on a predictable schedule.
Interval | Maintenance Task |
---|---|
3 months | Oil change, tire check |
6 months | Brake inspection |
12 months | Engine tune-up |
Usage-Based Maintenance
Think of this as maintenance triggered by mileage or hours of operation, based on how much your vehicles are actually used.
- Triggering maintenance after certain usage milestones: Perfect for vehicles that have variable operational loads.
Milestone | Maintenance Task |
---|---|
10,000 miles | Engine oil change |
20,000 miles | Transmission fluid change |
500 hours | Hydraulic system check |
Condition-Based Maintenance
Here, the focus is on the equipment’s actual condition, which can vary regardless of time or usage.
- Performing maintenance based on equipment condition: This might involve regular inspections and the use of sensors to monitor vehicle health.
Condition to Monitor | Maintenance Task |
---|---|
Tire tread wear | Tire replacement |
Brake pad thickness | Brake replacement |
Engine performance | Diagnostic check |
Implementing Preventive Maintenance in Fleet Management
Effective implementation of preventive maintenance requires thoughtful planning and the right tools. Here’s how to do it:
Planning and Scheduling
- Developing a preventive maintenance schedule: Outline all maintenance tasks and intervals based on vehicle type and usage.
- Importance of consistency and regularity: Regular maintenance helps avoid breakdowns and extends vehicle life.
Tools and Technologies
Leveraging modern technology can make preventive maintenance more efficient and less cumbersome.
- Overview of CMMS (Computerized Maintenance Management Systems): These systems help manage maintenance schedules, track repairs, and store vehicle history.
- How telematics and fleet management software assist in preventive maintenance: These technologies provide real-time data on vehicle conditions, helping to schedule maintenance based on actual vehicle use and condition.
Tool/Technology | Functionality |
---|---|
CMMS | Scheduling, tracking, and reporting on maintenance. |
Telematics | Monitoring vehicle usage and condition in real-time. |
Challenges and Solutions in Preventive Maintenance
Implementing preventive maintenance isn’t without its hurdles. Understanding these challenges and knowing how to address them can set the stage for a successful maintenance strategy.
Common Challenges
Initial Setup Costs
- Implementing a new maintenance system can be costly upfront. This includes the expenses for new software, tools, and equipment.
Training and Adaptation for Staff
- Staff may be resistant to change or require significant training to adapt to new processes and technologies.
Strategic Solutions
Leveraging Technology to Streamline Processes
- Investing in the right technologies, like CMMS and telematics, can significantly reduce the long-term costs and complexity of maintenance operations.
Regular Training and Updates for Maintenance Staff
- Ongoing training sessions ensure that maintenance teams are up-to-date with the latest techniques and technologies, making the transition smoother and more effective.
Interested in minimizing disruptions and extending the lifespan of your fleet?
Learn More About Our Solutions
Reach out to discover how Salcomms Trackers can tailor a preventive maintenance program that suits your specific needs.